Rethinking Surface Farming
Growing oysters can be backbreaking work. Harvesting heavy bags, constantly flipping and reflipping cages, and never-ending tumbling are among the tasks that require labor and attention on an oyster farm. Although floating bags and cages are the most common oyster farming techniques in Maine, there are other ways to grow oysters. A company based in New Zealand called FlipFarm developed an innovative farm system that streamlines the time-consuming aspects of oyster farming.
As innovative as the FlipFarm system is, the New Zealand water conditions it was designed for are very different from those on the Maine coast. Keith Butterfield, founder of Butterfield Shellfish in Yarmouth, ME, played a major role in helping FlipFarm develop the creative solutions necessary to adapt this technology to a new environment.
What is FlipFarm?
Instead of using cages or floating bags to hold the oysters, FlipFarm uses hexagonal mesh bags. These bags, which are called baskets, have a float attached to one side and an axle attached to the other. A longline runs through the axle of each basket to create rows of oysters.
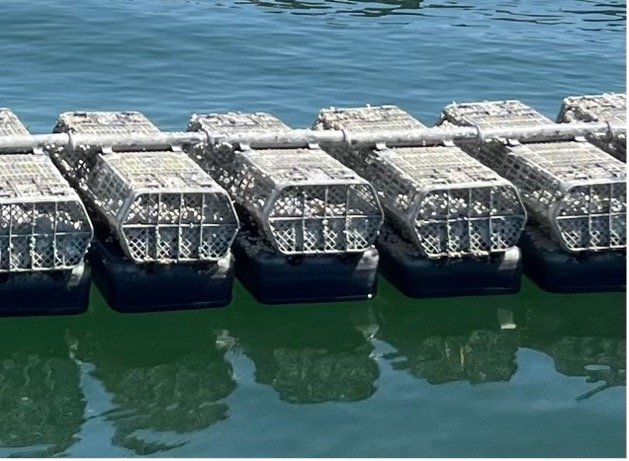
The axle, which is made of a short section of plastic pipe, allows the baskets to rotate 360 degrees around the line. This design means that growers can flip an entire line of oysters in just a couple minutes using a specialized catamaran called the helicat (“heli” for its helical shape and “cat” because it’s a catamaran). Harvesting and deploying, like flipping, use specialized equipment that allows the operation to run continuously instead of one bag or cage at a time. FlipFarm often compares the process of using their gear to the assembly line of a bottling plant, meaning it is continuous and repetitive.
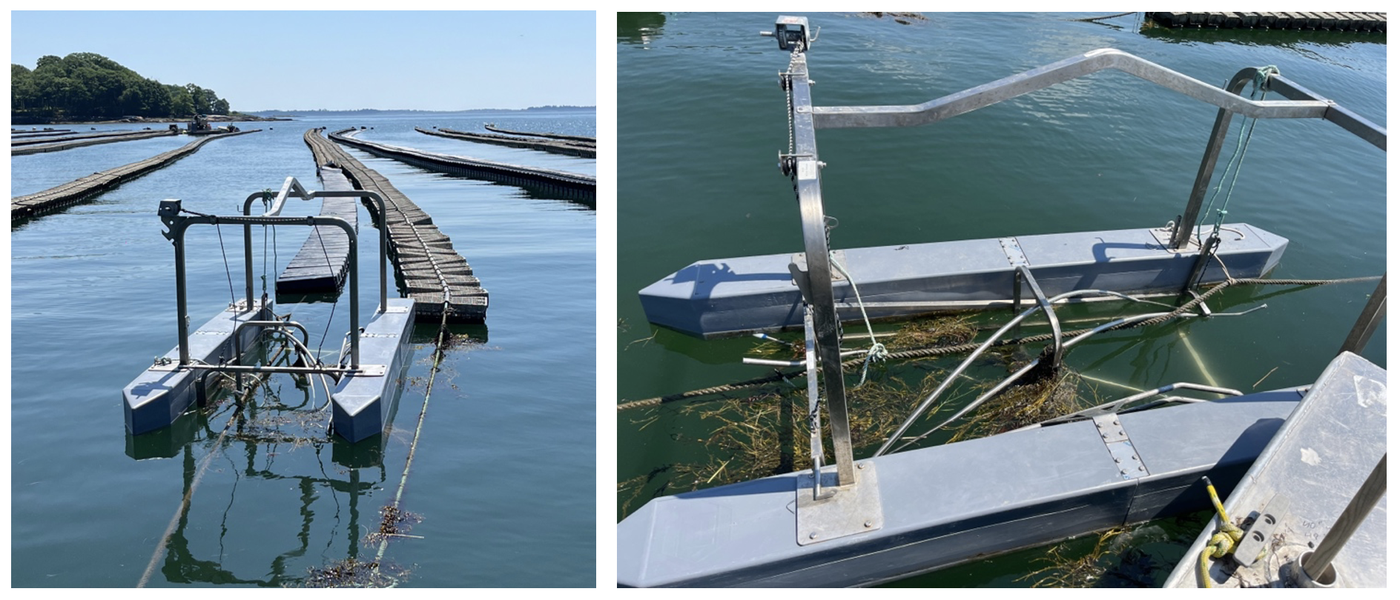
Developing More Robust Floats
The FlipFarm floats have come a long way since their original design. What was initially a rectangular piece of foam is now a specialized blown plastic float designed to meet the demands of large waves and heavy oysters.
The latest floats are made from reinforced and completely sealed blown plastic. The FlipFarm team switched from 9-liter (2.4 gal) floats to larger sizes to provide additional stability and ensure that baskets sit high enough to kill all biofouling (like mussels and sea squirts). In order to improve the baskets’ stability while they’re drying, one side of the float is slightly larger than the other. When in the drying position, the oysters fall to the side of the basket with the larger float. This keeps the baskets sitting level in the water and prevents them from flipping back over accidentally.
Improving the Axle Design
At Butterfield Shellfish, Keith found that some wave action is actually beneficial for growing oysters. Larger waves create a tumbling motion that is best for shaping oysters as they grow, and smaller waves are preferred for letting seed and smaller oysters grow quickly. To ensure that the FlipFarm gear was up to the task of growing in these wave conditions, the axle that attaches each basket to the longline had to be improved.
The brackets that attach the axle to the basket are sharp enough that wave action sometimes tore holes in the mesh. To address this, Hexcyl, the basket manufacturer, added additional reinforcement to the basket spine to strengthen the place where the axle is attached. Additionally, the bolts that held the bracket to the basket were replaced with much more robust stainless-steel rivets.
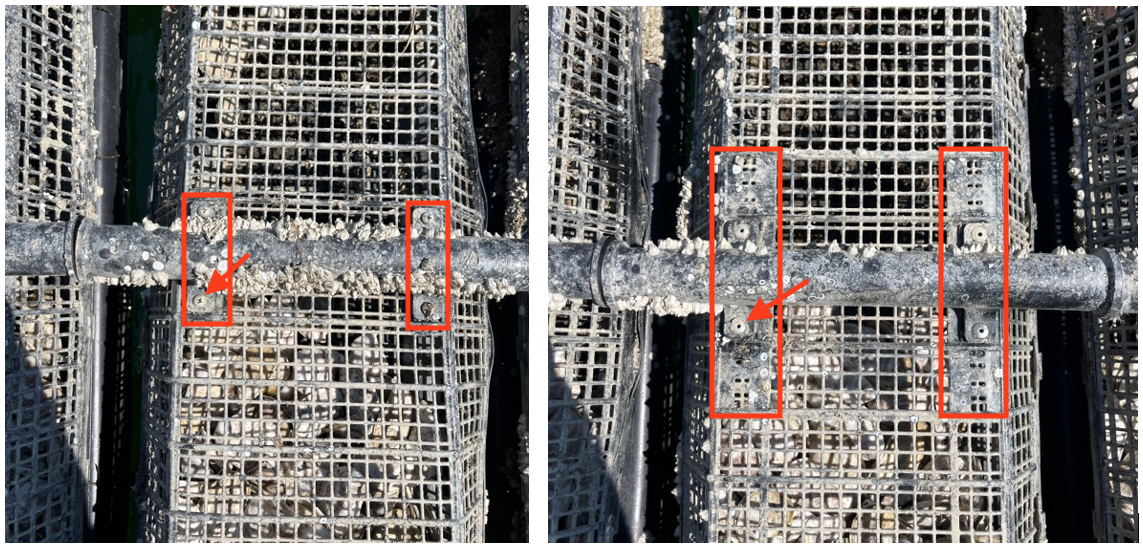
Growing Seed With FlipFarm
While the baskets come in a limited array of mesh sizes, there is a unique way to grow seed in the FlipFarm system. Bag inserts made with very small mesh can be used to grow seed inside the FlipFarm basket, as seen in the image below. The inserts are uniquely shaped to fit in these baskets and are attached with Velcro for easy deployment and harvesting.
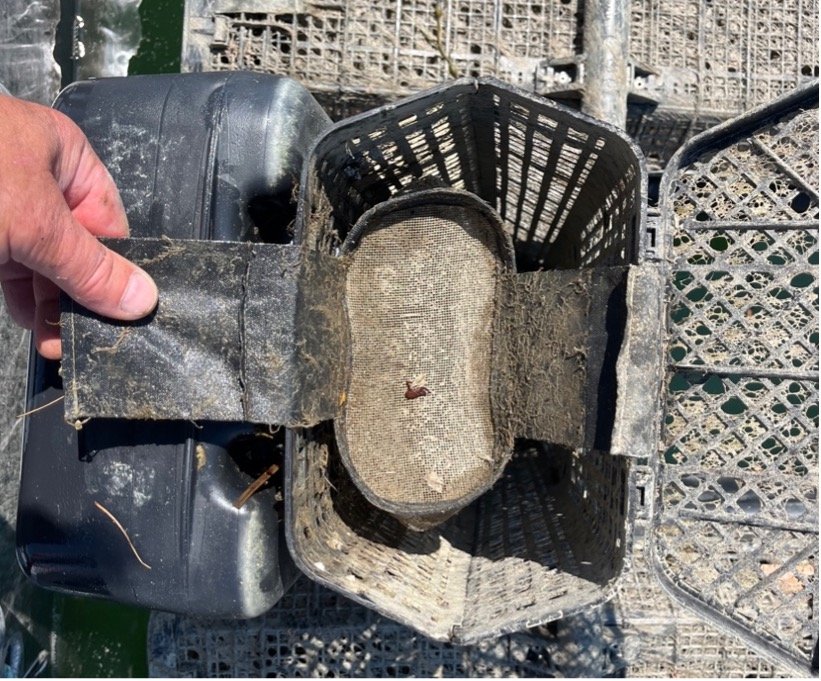
The System for Large and Small Farms Alike
In addition to their specialized baskets, there is a wide array of gear that FlipFarm sells for flipping, deploying, and harvesting. While this gear is part of what makes FlipFarm so efficient, the high upfront cost of buying all that gear is one of the biggest roadblocks to the use of this system today. However, for small growers and those who just want to test out a few lines of FlipFarm, there are still a lot of reasons why investing in the FlipFarm baskets could be beneficial.
Even without the harvesting and deployment gear, you can flip a whole line of baskets quickly by hand because after the first two baskets are flipped, the rest of the row easily follows (much like toppling a line of dominos). Filling baskets can be done from the boat by tipping each basket upwards individually, without the specialized deployment catamaran. Similarly, you can harvest by dumping each basket into a crate while driving a boat down the line. A few small farms could even share a helicat or other gear because each farm would only need to use it for a few hours every week.
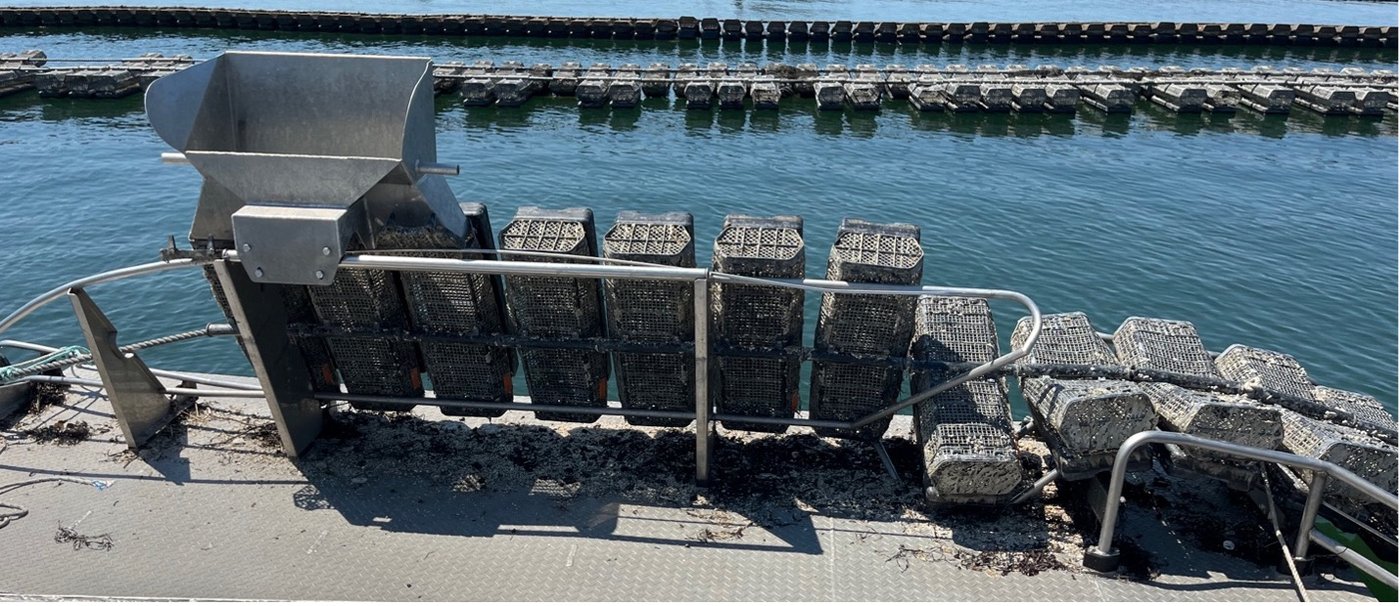
Future Advancements
Even with all the recent advancements in this technology, there are a few remaining kinks to work out. Figuring out how to sink baskets for overwintering or to weather storms has been particularly important. Butterfield Shellfish is testing out a prototype for sinkable floats that uses existing equipment and follows FlipFarm’s trend of minimizing the required labor. The design allows farmers to either fully or partially sink their oysters by filling the floats with varying amounts of water.
Developing a new farming technology requires creativity and diligence. The work that Keith and the FlipFarm team in New Zealand have done to adapt their farming system to the Maine waters are full of innovative and thoughtful solutions. They have come a long way and it will be exciting where they take this technology next.
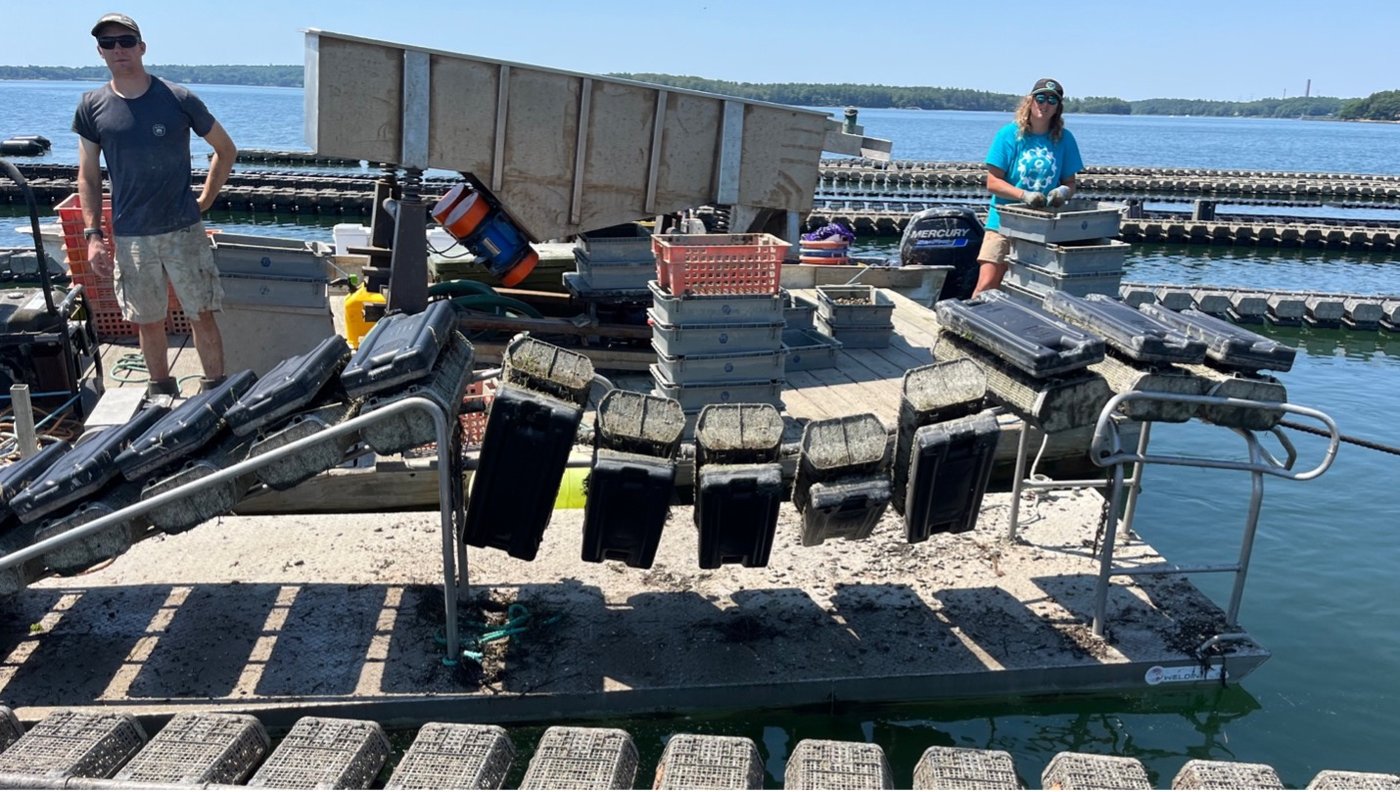
Innovations articles highlight creative devices and methods used on aquaculture farms. They are informed by farm visits and interviews with experienced growers. See our About page for more information.