Removing the Plastic From Oyster Farming
Oyster farming has a well-earned reputation for being environmentally conscious. At Deer Isle Oyster Company, Abby Barrows and Ben Jackson are pushing the industry forwards, to a future without the plastic that oyster growing equipment is usually made of. The gear they are prototyping on their farm covers a wide range of oyster growing husbandry and makes use of a variety of non-plastic materials.
As more research is done on how microplastics affect human health, plastic-free equipment might become a more important part of oyster farming. Plastic-free farming also helps growers expand their public image as environmental stewards. In addition to designing and testing plastic-free gear, Deer Isle Oyster Co. is giving individual growers the power to make their own plastic-free equipment. Their goal is to develop equipment that farmers and fishermen could make with tools they already have and materials they could buy at the hardware store.
Stainless Steel and Cedar Bags
The majority of oysters grown in Maine are cultivated in mesh bags made of marine grade plastic. There’s a reason these are the standard across the industry – they are light, cheap, and last a long time. In the woodshop, Ben Jackson has been prototyping oyster-bag alternatives made from non-plastic materials. The result is a stainless steel and cedar box designed to fit in the existing system for cage-grown oysters. The “bags” are made of folded stainless-steel mesh attached to cedar sliders with hog rings and staples. The pieces of cedar act as rails that allow the bag to slide in and out of cages relatively easily. Additionally, they have been working with aluminum mesh, as the interaction between different metal types in seawater causes corrosion. They are also looking at incorporating zinc to help reduce this inevitable break down of metal.
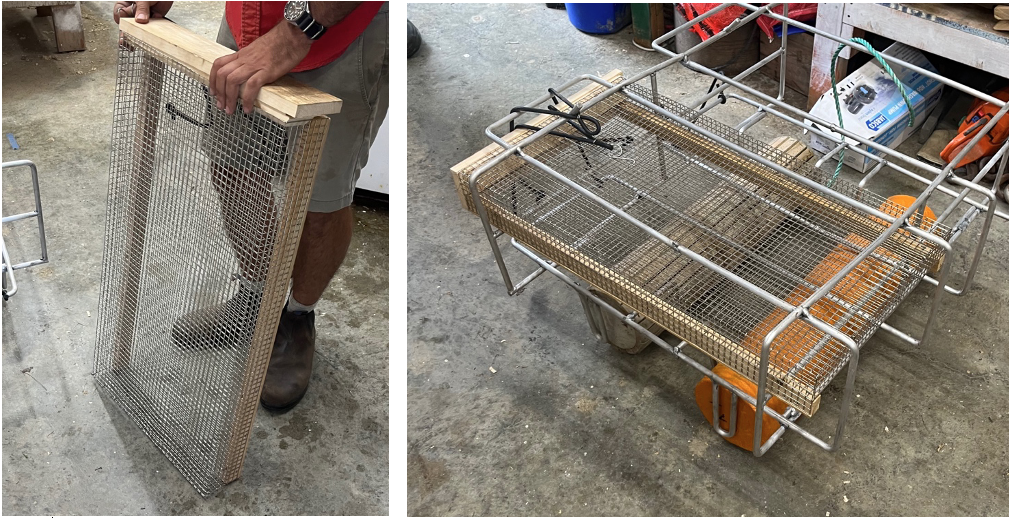
For growing seed, the stainless-steel mesh is replaced with durable window screen material called Pet Screen or stainless steel screen. Two screens are sandwiched inside a wooden cedar frame to create a bag with holes small enough to hold baby oysters fresh out of the hatchery. The wooden frame is held in place with aluminum clips fabricated in the shop. The clips slide into grooves cut into the exterior of the frame and hold the bag together tightly without the need for screws or fasteners. Using an oyster shucking knife clips can be pried out and the bag disassembled and reused over and over again.
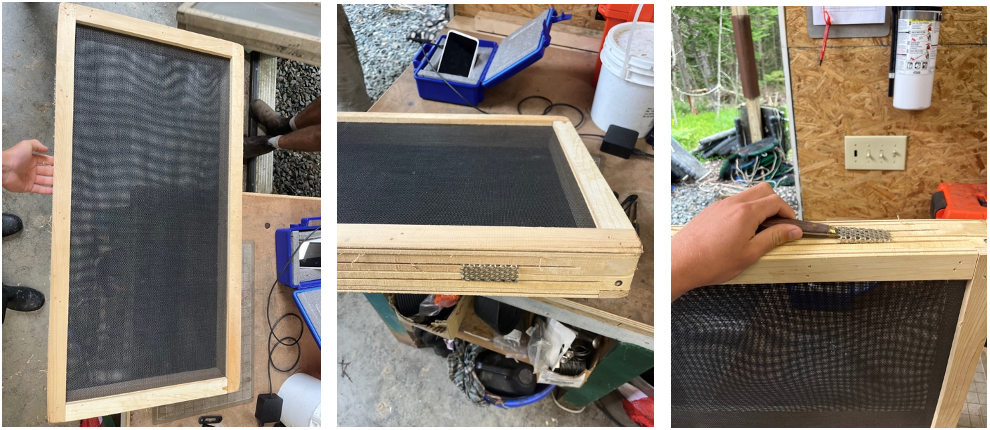
Plastic-Free Buoys and Floats
Plastic buoys have become the norm in most waterfront applications. One of the emerging plastic-free buoy alternatives is a mushroom-based buoy made by MycoBuoys™. The buoys are part of a research project into biodegradable, ecologically friendly alternatives to polystyrene plastic floatation devices. The buoys are grown using agricultural hemp waste and fungal mycelium (a general term for the roots of fungi). Once they’re grown, the mushroom buoys can be sealed with a biocompatible coating.
Deer Isle Oyster Company and the Hurricane Island Center for Science and Leadership are two of several testing sites for these buoys across the northeast U.S. The on-water testing efforts are aimed at developing a buoy and coating that can withstand the harsh marine environment for long enough to act as a viable replacement to the existing plastic buoys.
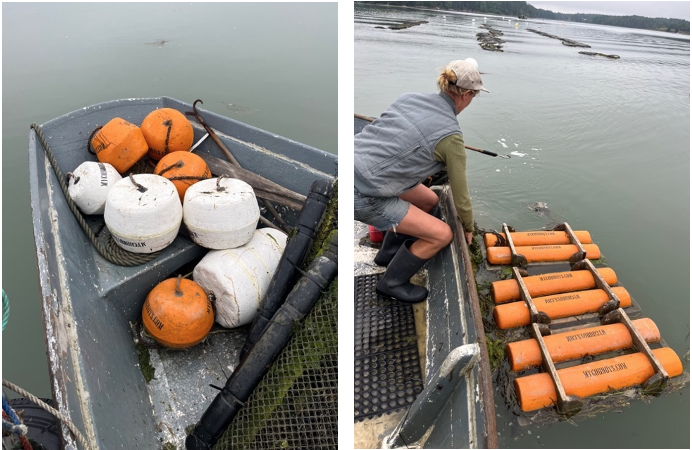
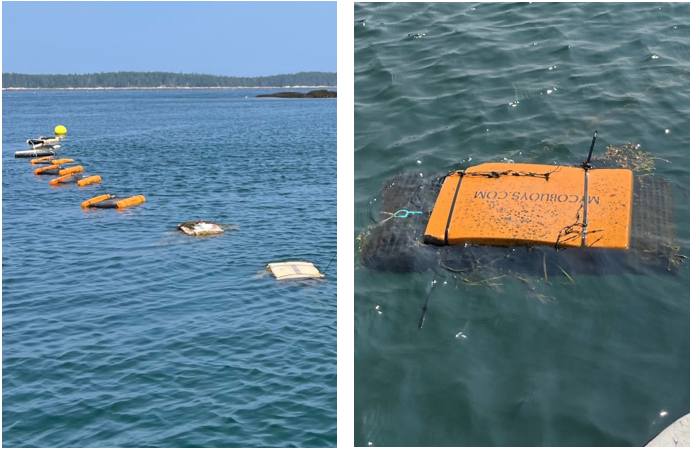
In addition to mushroom-based buoys, Deer Isle Oyster Co. is also developing wooden cedar floatation devices. Cedar is widely available and well known for its buoyant, water-resistant properties. The design they're testing could be manufactured at home by oyster farmers, eliminating the need to buy new floats at all. Additionally, they are looking into small aluminum pontoon-style buoys for floating 4- and 6-bay oyster gro ranches.
These prototype ideas for plastic-free floats may not be ready for market sale yet, but they demonstrate the progress of an industry that is dedicated to innovation and striving towards more sustainable gear.
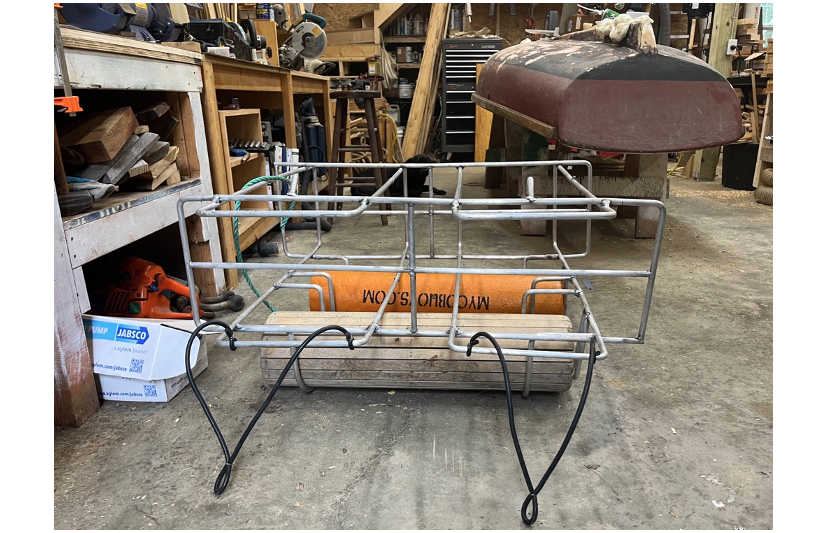
Aluminum Cages
Floating oyster cages are usually manufactured out of plastic-coated metal. While this design is rugged and tough, it includes a plastic component that isn’t really necessary to grow quality oysters. Some of the cages at Deer Isle Oyster Co. are made out of uncoated aluminum. The cages work in just the same way as traditional ones, but are manufactured without the plastic coating. The minimalist design reduces the amount of biofouling that can occur on the structure, meaning less frequent and quicker drying time for reducing fouling. The cages are also designed for use with a variety of floatation devices. Plastic floats are most commonly used, but other buoys could be used as drop-in replacements should a farmer decide to experiment with different flotation devices.
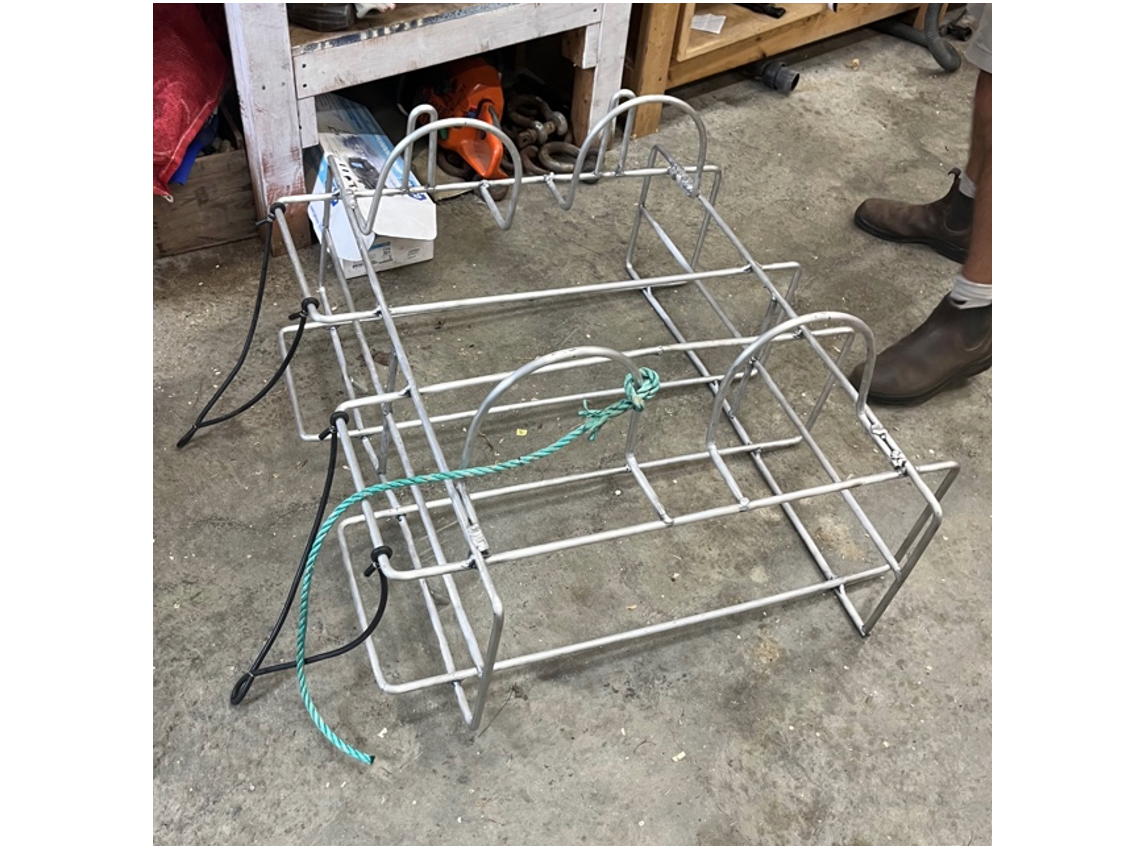
Reintroducing Wooden Lobster Crates
Many oyster farms use temporary storage or re-submergence system after harvesting. Storage offers more flexibility between harvesting and selling and can be used to ensure the freshest possible product. At Deer Isle Oyster Co, they use lobster crates to hold oysters next to their on-water float. In addition to using the typical plastic crate, they are testing wooden crates as well. Before plastic crates took over the market in the late 1990s, wooden lobster crates were the standard across the lobster industry.
In the lobster industry, plastic crates are superior for their consistent weight, which is important because lobsters are sold by the pound. For oysters, on the other hand, wooden crates might be a better choice. Crates are used just for temporary on-water storage, where the extra buoyancy provided by the wooden crates actually helps keep things afloat when full of oysters.
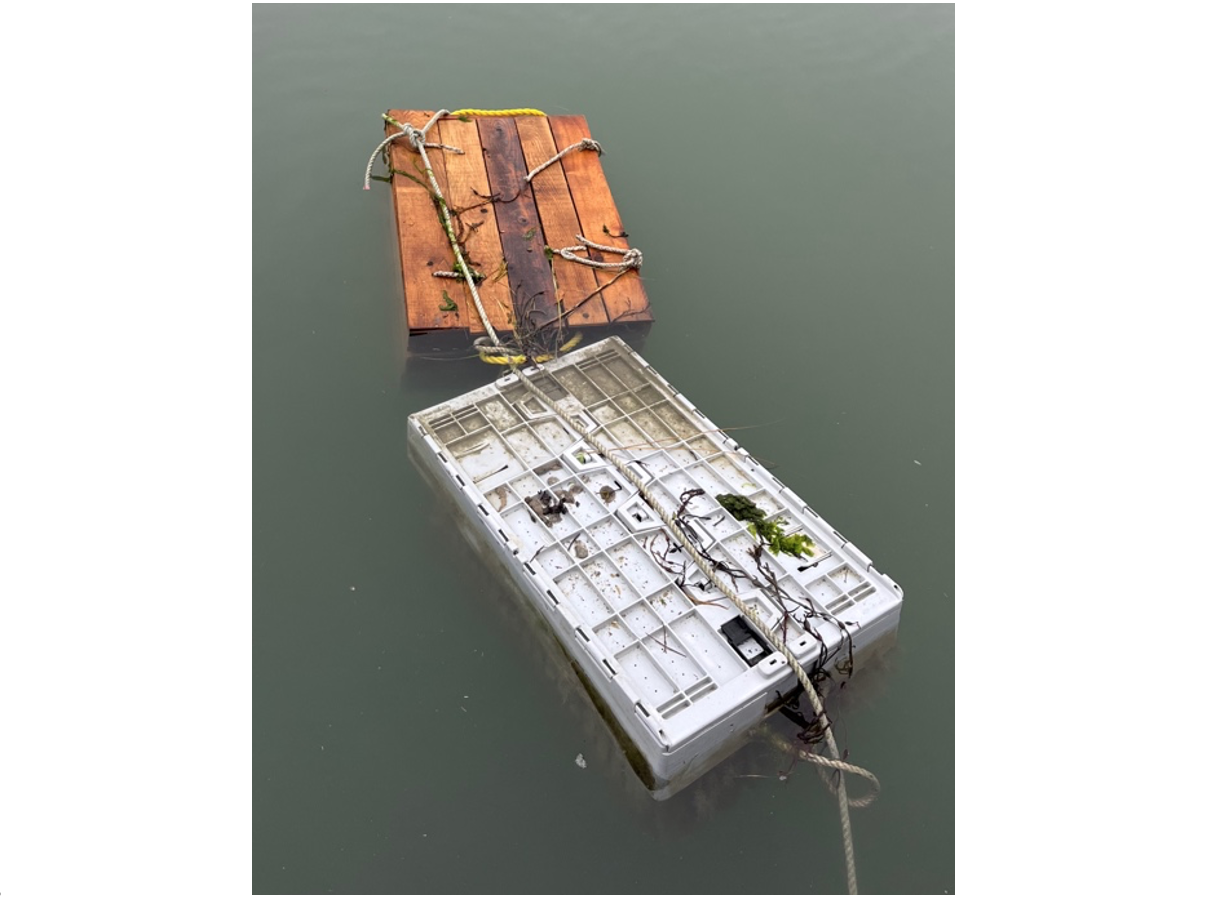
The Future of Plastic Free Oystering
The vision is that by developing plastic-free options for oystering, farms could slowly start to replace their plastic gear with other materials. Since the gear described in this article is designed as drop-in replacements for existing oyster equipment, farmers can transition gradually instead of making the switch all at once. As gear reaches the end of its lifetime, the goal is that growers could try plastic-free replacements instead of buying more plastics.
Abby and Ben constructed these devices using equipment farmers and lobstermen have easy access to. The idea is that they could be purchased but that the design and easily accessible materials would also allow farmers to make their own, benefiting the environment and their budget. Plus, a future with more people constructing plastic-free prototypes would spark more innovation down the line.
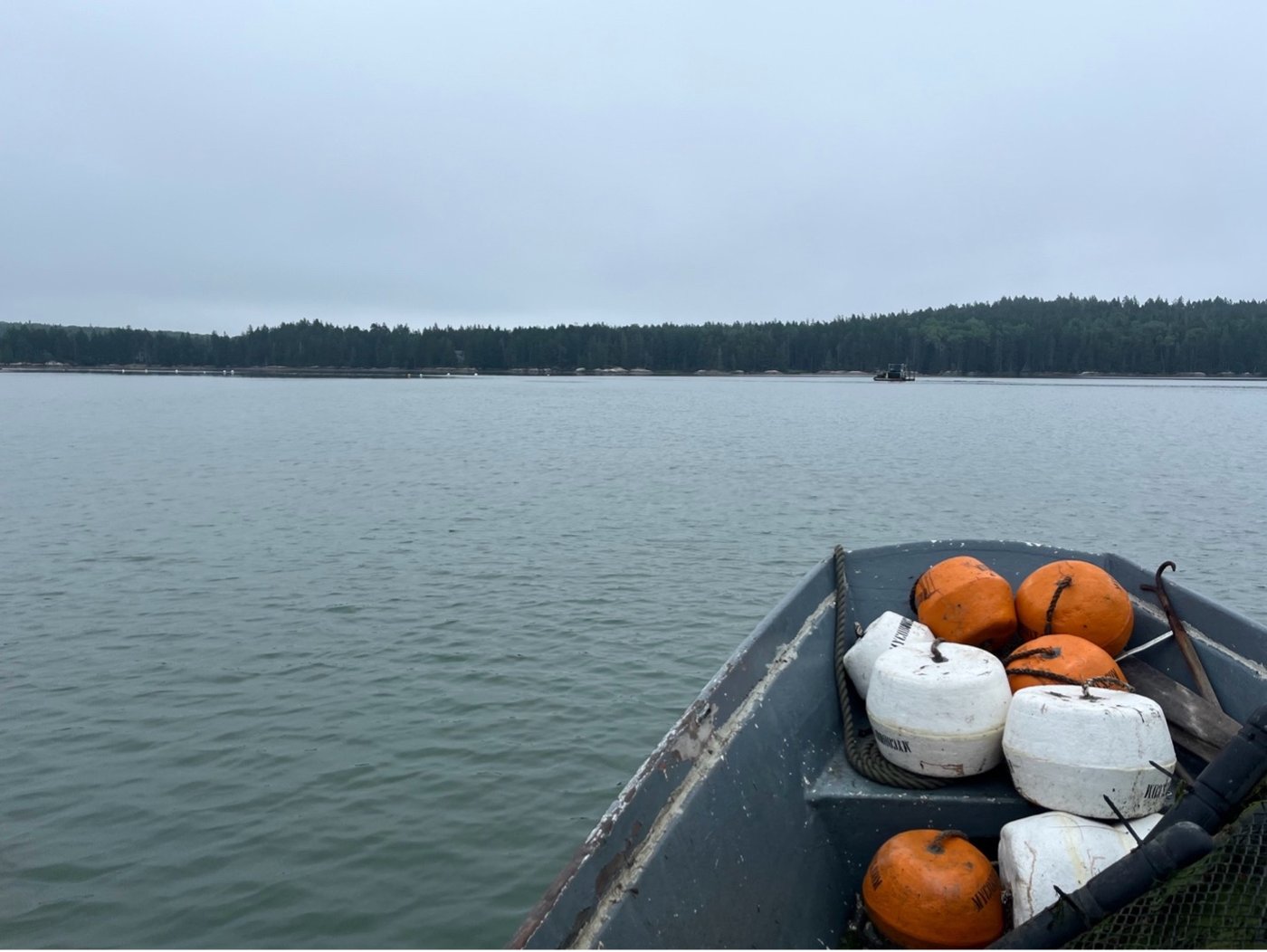
Innovations articles highlight creative devices or methods on aquaculture farms. They are informed by farm visits and interviews with experienced growers. See our About page for more information.