
Learn the Gear
Aquaculture gear types are species-specific and vary drastically in cost, site requirements, required labor, upkeep, and longevity. Gear will be one of your biggest business expenses (if you use it, that is), so pick the optimal equipment and farm layout the first time around.
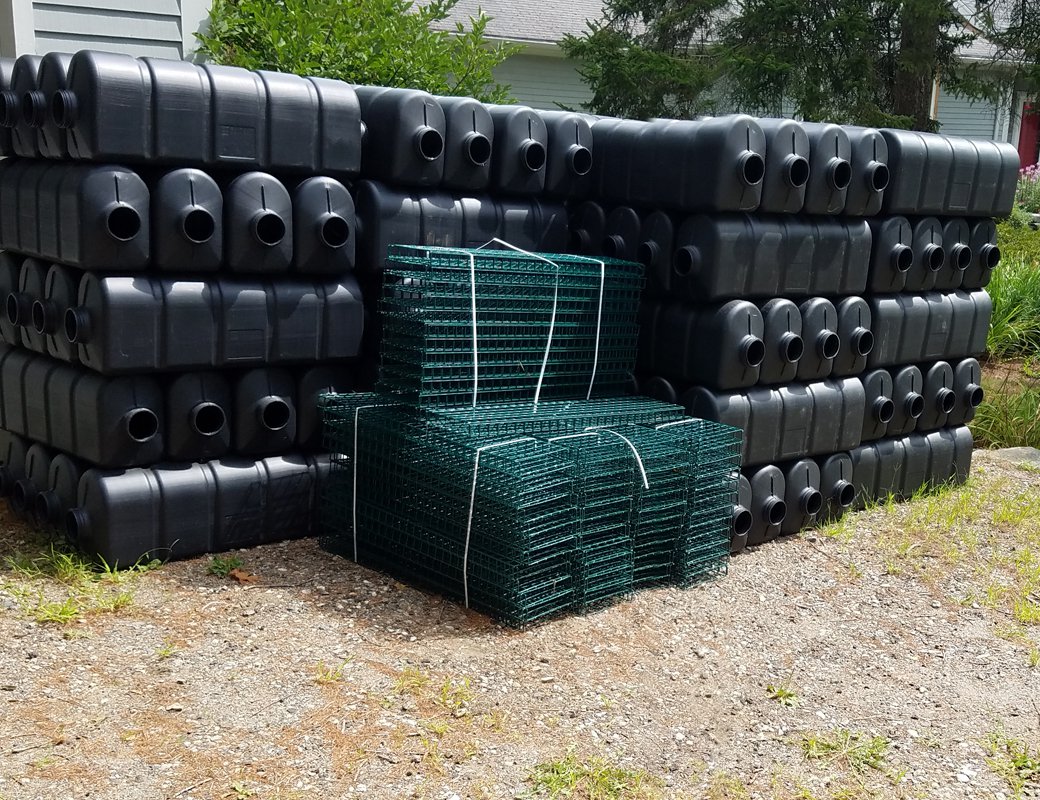
Questions
Oyster Gear
-
Oysters are typically grown either on the bottom with no gear, on the bottom in cages, or floating on the surface in bags or cages. Oysters grown on the bottom without gear are harvested by a small drag or by a diver by hand. In shallow or inter-tidal areas, bottom planted oysters can be accessed and harvested by foot. Bottom cages are typically wire shelves that hold several soft mesh bags that hold oysters. Floating cages are a series of shelves with floats on each side that hold 4 or more soft mesh bags with oysters inside. Floating bags are single bags with a float on each side that hold oysters. In addition to these tried and true methods, Maine growers are testing new methods of ‘flip bags’ that are similar to floating bags but use the tides (e.g., Zapco) or specialized implements (e.g., FlipFarm) to flip the bags.
-
Oyster farming equipment is less expensive than mussel gear and available locally. The biggest equipment costs are a boat, upweller, tumbler, work platform, cages/bags, moorings, and shore-side infrastructure. You don’t necessarily need an upweller, tumbler, and work platform when you start out; and you might choose to not use these at all depending on your growing techniques and size of your operation. Equipment costs for a startup commercial oyster farm will vary dramatically depending on scale but range from a few thousand dollars to $200,000+. Many of Maine’s commercial oyster farms successfully “bootstrapped” their farms and grew slowly, while others sought outside funding to achieve scale quickly.
-
A flat bottom skiff (e.g., Carolina Skiff®) is the boat of choice for cage and bag cultured oysters. The flat bottom provides a stable deck to work on and has room to hold bags, cages, and other equipment. Another benefit of the flat bottom skiff is the deck being at the water’s surface and low sides, which allows workers to lean over the side to access cages and bags. Lastly, this type of skiff can be outfitted with a davit, which reduces labor considerably. An oyster cage loaded with 1,500 market oysters is heavy! For bottom planted oysters a lobster-type boat, outfitted with a small drag, is commonly used.
Mussel Gear
-
The dominant method of growing mussels in Maine is raft culture, which involves attaching mussels to hanging lines that are connected to a floating raft (typically 40’ x 40’). There is one company in Maine that uses the Dutch style of bottom culture. For the purposes of this guide, we only cover the dominant method of raft culture.
-
Mussel farming is the most expensive because it requires multiple rafts (including dropper lines, predator nets, and moorings), a work barge or vessel, and several pieces of specialized stainless steel or aluminum processing equipment. This specialized equipment is not available locally, so shipping is a considerable additional cost. Equipment for a commercial scale, fully outfitted mussel farm will cost $200,000 - $1,000,000+. That said, markets for mussels are extremely strong and much of the priciest equipment will last a decade or longer, so despite the upfront costs, mussel farming might have the most sure-fire business model if done at the right scale.
-
A lobster-type boat, barge, and specialized mussel vessel are all used in Maine. The important thing is having a large, wide, stable platform that can hold the equipment, a crane, and Xactics totes.
Sea Scallops
-
Five years ago, mesh bags and Aquatrays were the method of choice, but this technique was found to be gear and labor intensive since scallops swim and clamp onto each other and therefore require a lot of space and low densities. Maine's industry has mostly shifted to pearl nets or lantern nets hung from a horizontal long-line and "ear hanging". Ear hanging – a widely used technique in Japan – uses specialized equipment to drill holes near the hinge, connect the scallops to a suspended vertical long-line on barbs, and remove biofouling without detaching the scallops from the ropes.
-
Cost and availability of pearl and lantern nets vary because they must be shipped from Asia, with minimum volume requirements and shipping costs. The full suite of specialized drilling, pinning, and washing equipment necessary for ear hanging costs from $75,000 upwards and is difficult to source without a contact in Japan. Our recommendation is to contact Coastal Enterprises Incorporated or Maine Sea Grant to understand costs and equipment purchase methods. Both of these groups have led the charge for the latest scallop farming innovations.
-
Depending on the technique, flat bottom skiffs (e.g., Carolina Skiff) or lobster-type boats are used. Similar to oyster farming, a skiff works well for cages, mesh-bags, and Aquatrays. Lobster-type boats work well for ear hanging and lantern/pearl nets because they are stable, have large decks, and a hauler that can raise the lines.
Kelp Gear
-
Kelp is grown on horizontal longlines that are submerged approximately 7’ underwater. These longlines are secured to the seafloor with moorings and maintain their depth with surface buoys for floatation. At harvest, longlines are lifted out of the water by a hauler, mast and boom, powerblock, davit, or hand-winch and kelp fronds are cut off by hand.
-
Compared to shellfish and finfish aquaculture, kelp farming is relatively less expensive. The three primary gear costs are for: ropes, buoys and moorings. Moorings are typically the biggest expense outside of the work vessels. Mooring costs include: the anchors themselves, mooring chain, shackles, polyball mooring buoy, and sometimes a diver to service the gear, typically at the beginning and end of each season.
-
A 30’- 45’ lobster-type boat with a hauler and a skiff with a davit. The skiff is very useful for seeding, setting the kelp farm up in the fall, and monitoring the lines during the growing season. The larger boat, hauler and davit are necessary for efficient harvest operations.
Gear Resources
-
-
Visit How a High Tech Mussel Farm Harvests 7,000 Pounds of Mussels per Day
-
-
-
Visit How to Install a Soft-shell Clam Farm
-
Visit Oyster Production Equipment Comparisons 2016–2018
Oyster Production Equipment Comparisons 2016–2018
The report provides information on commercially relevant aspects of oyster production gear associated with each equipment type employed including, BST™ Crosshatch, BST™ Longline, OysterGro, Rack and Bag, & Seapa™. They tracked oyster survival, growth by season, shell morphology, worm presence, and cost estimates.2020Maryland Sea Grant, University of Maryland